Brief Intro of Centrifugal Fan
Centrifugal fans are essential equipment in ventilation, air handling, dust extraction, and process cooling systems. Unlike axial fans, which move air in a straight line, centrifugal fans redirect airflow radially, allowing for higher static pressure and greater efficiency in ducted systems.
At Zhejiang Shuangyang Fans Holding Co., Ltd, we specialize in manufacturing high-performance centrifugal fans for applications in subways, tunnels, power plants, factories, and high-rise buildings.
Basic Working Principle
A centrifugal fan works by drawing air into the fan inlet and using a rotating impeller to accelerate the air radially outward into a scroll-shaped fan housing. The resulting increase in velocity is converted into pressure, making it ideal for medium to high-pressure systems.
The performance of a centrifugal fan heavily depends on the aerodynamic and mechanical structure of its core components.
Key Structural Components of a Centrifugal Fan
The major components of a centrifugal fan include:
-
Impeller
-
Inlet Cone
-
Fan Housing (Scroll or Volute)
-
Drive Mechanism (Direct or Belt)
-
Motor
-
Base Frame or Mounting Assembly
-
Bearings and Shaft
-
Accessories: Dampers, Vibration Isolators, Silencers
Each part contributes to the fan’s stability, noise level, airflow efficiency, and adaptability to application requirements.
Impeller: The Heart of the Fan
The impeller is the most critical part of the centrifugal fan. It consists of blades (or vanes) mounted around a central hub and can be classified into four main blade types:
-
Backward curved (BC)
-
Backward inclined (BI)
-
Forward curved (FC)
-
Radial (straight blade)
Each blade design serves different pressure and airflow needs. For instance, backward curved blades offer high efficiency and low noise, making them suitable for HVAC systems and industrial air handling. Forward curved blades are compact and used in low-pressure environments, such as small air handlers or cabinet units.
Materials commonly used include carbon steel, stainless steel, aluminum, or composite resins, depending on corrosion resistance, temperature, and mechanical strength needs.
The impeller is dynamically balanced to reduce vibration and extend bearing life, especially for large-diameter fans.
Inlet and Outlet: Controlling Airflow
The inlet cone or inlet box directs air smoothly into the impeller, reducing turbulence and improving efficiency. For high-performance applications, aerodynamic inlet designs help optimize pressure recovery.
At the outlet, the volute housing collects and redirects the air from the impeller to the duct system. The volute geometry ensures efficient transformation of kinetic energy into static pressure.
Fan Housing and Mounting Base
The fan housing, typically scroll-shaped, is designed to match the airflow path and minimize energy loss. The housing can be:
-
Single-width single-inlet (SWSI)
-
Double-width double-inlet (DWDI)
DWDI designs are used where large volumes of air are needed, such as HVAC air handling units (AHUs).
The housing is often constructed with galvanized steel or powder-coated carbon steel. In corrosive or high-temperature environments, stainless steel or coated materials are applied.
The mounting base provides structural integrity and often includes vibration isolators to prevent noise and mechanical wear, especially in roof-mounted or mechanical room installations.
Drive Mechanism: Belt or Direct Drive
There are two common drive methods:
Direct-drive:
The motor is directly coupled to the impeller shaft. It offers high reliability, low maintenance, and compact structure—ideal for clean-air systems.
Belt-drive:
Allows adjustment of fan speed by changing pulley sizes. Belt drives are preferred when variable airflow is needed or the motor must be isolated from high-temperature or contaminated air.
High-performance fans may include variable frequency drives (VFDs) or EC motors for energy-efficient control.
Accessories and Structural Enhancements
To enhance performance and durability, centrifugal fans often include:
-
Flexible connectors: Minimize vibration transmission to ductwork
-
Backdraft dampers: Prevent reverse airflow during system shutdown
-
Access doors: Facilitate inspection and maintenance
-
Sound attenuators or silencers: For noise-sensitive environments
-
Thermal insulation jackets: In HVAC or process systems involving temperature control
These structural elements are integrated into the design to meet industry standards.
Conclusion
The structure of a centrifugal fan is a combination of aerodynamic design, mechanical engineering, and material science. Each component—from impeller blades to housing geometry—affects how the fan performs in demanding environments.
At SHUANGYANG FAN, we design and manufacture centrifugal fans that meet the highest industry standards for performance, safety, and reliability. Whether it’s a ventilation project or a factory dust collection system, the right structure ensures long-term efficiency and minimal downtime.
Note: The content of the article cannot avoid omissions and errors. Welcome to propose corrections.
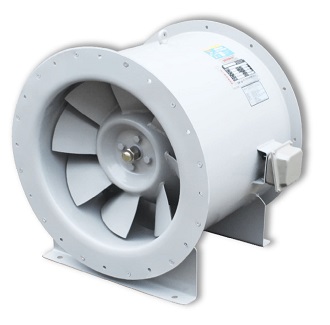
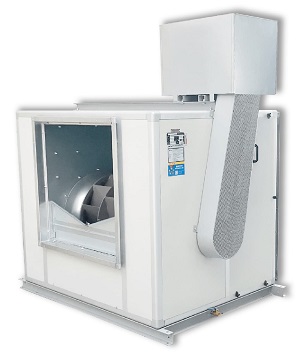
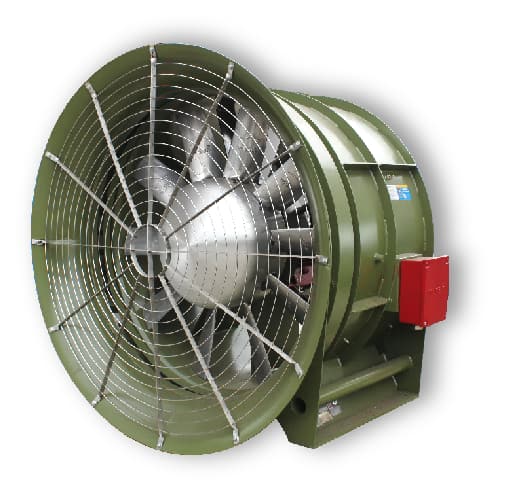
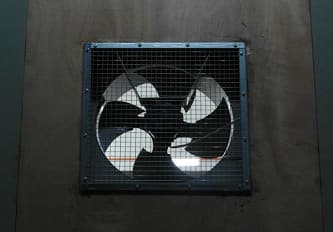